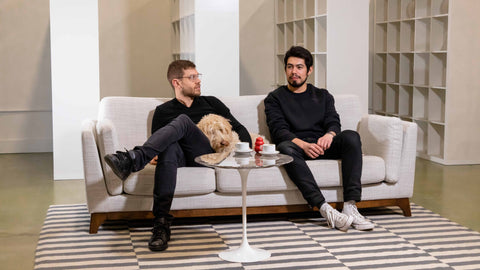
- Tell us something about your Look Book designs that we can't see from the photos.
We print every piece of glass in house. We have the opportunity to customize and create a unique design for each project. So, one of the elements photographs can't convey is the design freedom our studio has. Also, because the lights we make often have a kinetic element, the fluid movement of light patterns is, obviously, only implied by still photos. Sometimes a short video is needed to get the feeling of the work.
- Tell us something about your Look Book designs that we can't see in photos.
We print each piece of glass in-house. We have the opportunity to customize and create a unique design for each project. So one of the elements that photographs don't capture is the creative freedom we have as a design studio. Also, as the lamps we make have kinetic elements, the fluid movement of light patterns is not fully appreciated in still images, so a short video is sometimes required to get the feel of the work.
- What inspired you to go into lighting and glass? What is your background that got you into the design process?
Our desire to print glass developed in MIT's glassblowing studio. As a college student at MIT, I started taking classes at the MIT Glass Lab and I fell in love with this material. Later as a graduate students, Daniel and I had the opportunity to collaborate with an incredible team on the development of experimental glass printing technology. Looking back, it feels like this synergy of technology and traditional glass techniques was perfectly supported by our design backgrounds in mechanical engineering and architecture.
- What inspired you to pursue lighting and glass? What is the background of your foray into the design process?
Our desire to print glass was developed in the blowing studio at MIT. As an undergraduate at MIT, I started taking classes in his glass studio and fell in love with the material. Later, after we graduated, Daniel and I had the opportunity to collaborate with an amazing team in developing an experimental technology for printing on glass. Looking back, it feels like the synergy of technology and traditional glass techniques were perfectly complemented by our knowledge of mechanical engineering and architecture.
- Where do you get your ideas for the unique shapes? Is the glass pattern printed or blown?
We both teach and blow glass regularly (or, it was regular before covid paused the world), which keeps us intimately involved with the material. We see the printing technology as an extension of our embodied knowledge of our material, finding inspiration from the emerging and inherent properties of glass. We try to simultaneously remain respectful of the glass's natural abilities while asking what can we create with this technology that no one has ever seen before and can't be made any other way?
- Where do you get your ideas for such unique shapes? Is the pattern on the glass printed or blown?
We both teach and work with blown glass regularly (or it was regularly at least before COVID brought the world to a halt), which keeps us intimately involved with the material. We see printing technology as an extension of our very embodied knowledge of the material, drawing inspiration from the inherent and emergent properties of glass. Simultaneously we try to respect its nature and natural abilities, while asking ourselves what we can create with this technology that no one has ever seen or done before.
- How are your designs produced and where?
Our work starts with a concept or a natural inspiration. We take these ideas and craft them into digital parametric models. The digital designs are only a single curve in 3-dimensional space, representing a form and the spatial choreography that the printer
will trace to realize the final glass objects. When we are satisfied with the digital designs and the code is ready, we head to the hot shop where our printer lives and fire it up, a three-day process. Over the next two weeks we will print around 30 objects, feeding the printer with molten glass, carefully observing the printing, and slowly cooling each object. After we complete the hot work, we finish each piece of glass by grinding and polishing it's top and bottom plans and then pairing it with custom hardware.
- How and where are your designs produced?
Our work begins with a natural source of inspiration or a concept. We take these ideas and transform them into parametric digital models. The digital designs are only one aspect in three-dimensional space, they represent the shape and spatial choreography that the printer will trace to make the final glass pieces.
When we are happy with the digital design and the code is ready, we send the parts to the forge where the printer is and turn it on, this process takes 3 days.
Over the next two weeks around 30 objects are printed, feeding molten glass into the printer, carefully observing the printing process and slowly cooling each piece. After the heat work, we finish each piece by polishing its upper and lower planes and they are matched with custom-made molds.
- What do you have in mind for future designs? What is your evolution process?
We work to ask new questions of the glass, light patterns, technology, and ourselves with each design. Every time we fire up the printer, we have the opportunity to learn new things and to explore new directions. Our current focus is on a generatively designed series of over 800 designs for unique, organic shapes. From this set, we will select 12 that have characteristics we're most excited about and print them.
- What do you have in mind for future designs? What is its evolution process?
In each design we rethink new ideas regarding glass, light patterns, technology and ourselves.
Every time we turn on the printer, it's a new opportunity to learn new things and explore new paths.
Our current focus is on designing an abundant new series of over 800 designs in unique and organic shapes. From this series we will select the 12 that excite us the most and we will produce them.
Wanted Design Interview with Lios Design
- What role does your location play in your creative inspiration?
We started our practice as a spin off to continue experimenting with digital glass design, which we developed at the MIT Media Lab. Our design education came from that community and glassblowing from the MIT Glass Lab. We keep close ties with colleagues and mentors, nearly all of whom remain sources of inspiration and we love being able to interact and learn from the design, engineering, and glassblowing communities in Cambridge. Our studio is also adjacent to Almost Perfect Glass, a traditional glassblowing shop (where we actually fabricate 3D printed glass) that houses a number of local artists who we are lucky enough to work alongside and learn from.
- What role does the town you live in play for your creative inspiration?
We started working as an alternative to continue experimenting with digital glass design, which we developed at the MIT-Media Lab. Our design training comes from this same community, as well as that of blown glass from the MIT-Glass Lab. We maintain a Close contact with our peers and mentors, almost all of whom are a source of inspiration, we love being able to interact and learn from these Cambridge glassblowing, engineering and design communities. Our studio is also parallel to Almost Perfect Glass, a traditional glass blowing shop (where we fabricate and 3D print glass) which is home to a number of local artists whom we are fortunate to learn from and work with.
- As a designer, is form or function more important, or both?
In short, both, but our method is to question the nature of functionality through material exploration and particularly through unique methods of fabrication. If we rethink how we make things and what we make them from, what new typologies for design result?
- As a designer, what is more important, form, function or both?
In short, both. However, our method consists in asking the nature of the functionality through the exploration of the material and particularly through the exceptional manufacturing methods. If we reconsider the way we create and where it comes from, what new typologies for design would result?
- Has the pandemic affected your design and production? If so how.
As a two person studio, we already had the flexibility to work from home when possible and keep each other safe when doing physical making, something we are very thankful for. But of course, the slow down in projects brings both an added stress and extra space to think freely about new concepts and designs.
- Has the pandemic affected your design and production flow? If so, how?
Being a two person studio, we already had the flexibility to work from home when possible and we kept each other safe when it came to physical production, for which we are very grateful. But, unsurprisingly, the delay in projects left us with both additional stress and extra space to think freely about new concepts and designs.
- What artists/designers inspire you most that influence your design?
Those who exhibit a humility to material and curiosity to function. Tokujin Yoshuoka, Toots Zinsky, Roni Horn, Eero Saarinen, Alexander Calder, Neri Oxman, Tomas Seraceno, Kenzo Tange.
- Which artists/designers inspire you the most and influence your design work?
Those who demonstrate humility in the material and curiosity in the function: Tokujin Yoshuoka, Toots, Zinsky, Roni Horn, Eero Saarinen, Alexander Calder, Neri Oxman, Tomas Seraceno and Kenzo Tange.
- If you had to pick one, what would be your favorite design piece to date?
Daniel – absolutely couldn't pick one and stick with my answer for very long Michael – My favorite design is Tetra. The glass has this sharp, crystalline form and the light patterns it produces are a satisfying contrast of surging curves. I'm also incredibly excited about our new Morphogenesis Series, as yet only realized in the digital space. Stay tuned until the fall when we print them!
- If you had to choose one, what would be your favorite piece of design?
Daniel- I definitely couldn't choose just one and stay with that answer for a long time. Michael – My favorite design is Tetra. Glass has this sharp, crystalline shape and the patterns of light it produces make a satisfying contrast to the curves that emerge from it. I am incredibly excited for the Morphogenesis Series, so far only done in a digital space. Stay tuned for fall when we print them!
![]() |
![]() |
![]() |
![]() |